- Joined
- Jul 3, 2023
- Messages
- 28,077
- Reaction score
- 0
- Points
- 36
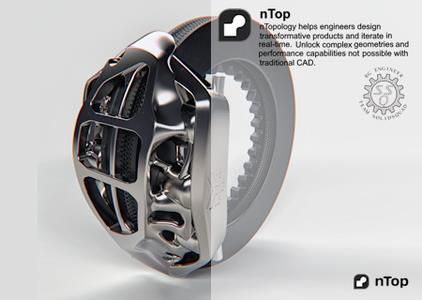
Free Download nTopology 4.25.2 | 1.7 Gb
nTopologyis pleased to announce the availability ofnTopology 4.25.2. This release features our new manufacturing constraints: 3-axis milling constraint and 5-axis milling constraint.
Owner:nTopology
Product Name:nTopology
Version:4.25.2
Supported Architectures:x64
Website Home Page :www.ntop.com
Languages Supported:english
System Requirements:Windows *
Size:1.7 Gb
nTop 4.25 - What's New
3-Axis Milling Constraint
The 3-Axis Milling Constraint block enables three-axis milling constraints on Topology Optimizations. The constraint ensures the Topology Optimization result can be manufactured without contact between the tool head and the design domain. It ensures no features are generated smaller than the smallest cutting tool would allow.
- Block Name: 3-Axis Milling Constraint
- Location: Beta > Topology Optimization
- The block has the following inputs:
. Head Radius: The radius of a half sphere used to represent a simplified drill chuck. This will ensure the cutting tool can access specific regions without interference. The head radius should be larger than the min tool radius.
. Tool Length: The length of the cutting tool, measured from the tip to the drill chuck.
. Min Tool Radius: The radius of the cutting tool. This input controls the radii that can occur in the results.
. Approach Directions: These are the possible milling directions. If left blank, the default directions are +X, -X, +Y, -Y, +Z, and -Z. You can select multiple approach directions for one milling configuration to allow for multi-sided machining.
- Output: Optimization Constraint
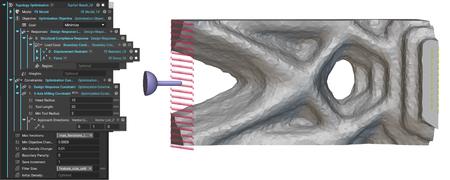
The above image shows an example of a Cantilever Beam optimized using the 3-Axis Milling Constraint on one axis.
5-Axis Milling Constraint
The 5-Axis Milling Constraint block enables five-axis milling constraints on Topology Optimizations. The constraint ensures the Topology Optimization result can be manufactured without contact between the tool head and the design domain. It ensures no features are generated smaller than the smallest cutting tool would allow.
- Block Name: 5-Axis Milling Constraint
- Location: Beta > Topology Optimization
- The block has the following inputs:
. Head Radius: The radius of a half sphere used to represent a simplified drill chuck. This will ensure the cutting tool can access specific regions without interference. The head radius should be larger than the min tool radius.
. Tool Length: The length of the cutting tool, measured from the tip to the drill chuck.
. Min Tool Radius: The radius of the cutting tool. This input controls the radii that can occur in the results.
- Output: Optimization Constraint
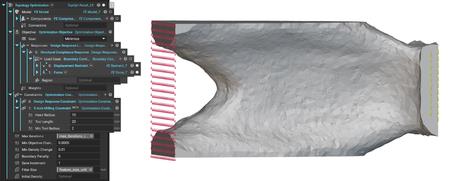
The above image shows an example of a Cantilever Beam optimized using the 5-Axis Milling Constraint.
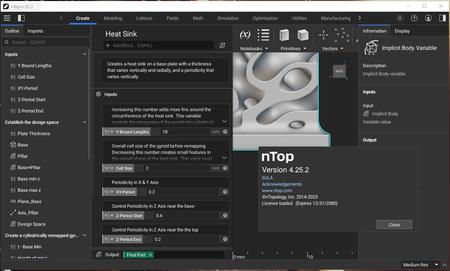
nTopologyintroduced the concept of implicit modeling for mechanical design, which is an innovative, modern, and scalable way define parts and products. It has many benefits to end-users and companies, such as the elimination of model failures, speed of changes or iterations, and scalability to name a few. But implicit modeling enables so much more. In this informational session, we'll explore a topic that is redefining product development - field-driven design. In short, field-driven design is a way for design, analysis, and manufacturing teams to overlay information into one engineering model. This approach enables orders of magnitude increase in design iteration speed and greatly improves collaboration between teams.
How Field-Driven Design Allows Engineers to Design for Additive Manufacturing
Watch this information session where we'll define field-driven design, show examples of how it enables better knowledge sharing, and show how it promotes the development of more sophisticated, highly engineered products. You'll also better understand how nTopology is addressing today's engineering problems through its nTop Platform product.
nTopologywas founded in 2015 to enable engineers and designers to create any geometry - no matter how complex - and meet the requirements of high-performance products.
Buy Premium From My Links To Get Resumable Support,Max Speed & Support Me
Rapidgator
http://peeplink.in/8b5e9eeb186e
Uploadgig
c1qdm....setup.rar
Fikper
c1qdm....setup.rar.html
Links are Interchangeable - No Password - Single Extraction